Unraveling the Triggers of Workplace Accidents
- Erone
- Jun 5, 2023
- 3 min read
Unmasking Workplace Dangers: A Lesson from the Odisha Train Accident

Industrial incidents and accidents don't just happen out of the blue. They are the culmination of several interconnected factors that together create a chain reaction leading to unfortunate events. These triggers can be grouped into three main categories: Human factors, Environmental factors, and Organizational factors.
The recent massive three-train collision that occurred in Odisha, India, on June 2nd, 2023, stands as a stark reminder of the urgency of understanding these triggers to prevent future incidents.
01. Human Factors: The Worker's Role in Safety

➤ Training Deficiency: Workers lacking adequate training in machinery operation, equipment use, or industrial processes are at an elevated risk of initiating or becoming victims of accidents. The train collision in Odisha underscores the importance of proper training in reducing incident likelihood.
➤ Non-adherence to PPE Usage: The refusal to use, or incorrect usage of, Personal rotective Equipment (PPE) can expose workers to injuries, especially in industrial settings where hazards are commonplace.
➤ Exhaustion and Stress: Overburdened, fatigued, or strained workers are more prone to errors, escalating the probability of incidents and accidents.
➤ Complacency and Overconfidence: Workers who are overly familiar with their tasks may become complacent and overlook potential risks, leading to accidents. Similarly, overconfidence can lead to workers underestimating the dangers associated with their work or neglecting safety procedures.
➤ Distractions: Distractions can lead to workers not paying full attention to their tasks, leading to mistakes and potential accidents. This can include anything from personal distractions, like personal phone use, to work-related distractions, like multi-tasking or noisy work environments.
Addressing these human factors requires a combination of proper training, fostering a culture of safety, providing support for workers dealing with fatigue and stress, and establishing procedures that minimize distractions and complacency.
02. Environmental Factors: The Workplace Atmosphere
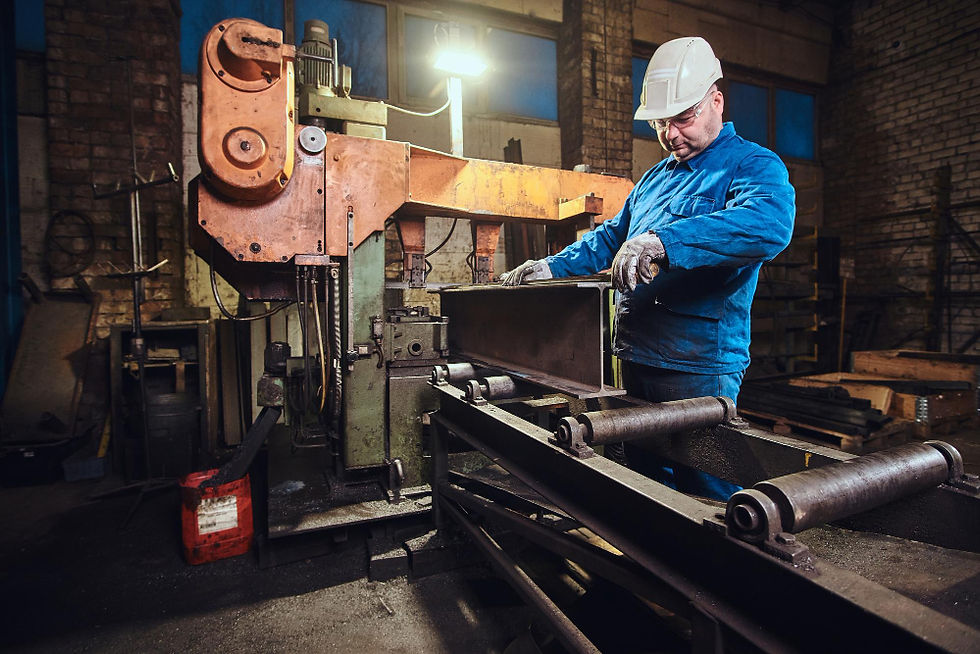
The physical and external conditions of the workplace also play a significant role in industrial incidents and accidents. Here's what to watch out for:
➤ Unsafe Conditions: Hazards like slippery floors, unstable structures, blocked walkways, poor lighting, or insufficient ventilation can make safe task execution challenging, thereby increasing accident potential.
➤ Equipment Failure: Neglected machinery, tools, or equipment can malfunction or break down, resulting in unexpected incidents that might harm workers or cause further damage.
➤ Hazardous Substances: Improper storage, handling, or control of potentially harmful substances such as chemicals, gases, or dust can pose severe health and safety risks.
➤ Extreme Temperatures: Both high and low temperatures can impair a worker's ability to function safely and effectively, leading to heat stress, dehydration, frostbite, or hypothermia.
➤ Noise Pollution: Prolonged exposure to high noise levels can lead to hearing damage, increase stress, distract workers, and elevate the risk of mistakes.
➤ Poor Housekeeping: A disorderly workspace can introduce a range of hazards such as trip and fall risks, fire hazards, or hindrances in locating safety equipment during emergencies.
Mitigating these environmental factors requires regular safety audits to identify potential hazards, effective maintenance of equipment, appropriate storage and handling of hazardous substances, controls for extreme temperatures and noise, and a commitment to maintaining a clean and orderly workplace.
03. Organizational Factors: The Role of Management

The structural and managerial aspects of the workplace contribute significantly to the
occurrence of incidents and accidents.
➤ Safety Culture: If safety is not prioritized at all managerial levels, employees may not take it seriously, leading to heightened accident risk.
➤ Communication: Clear and effective communication of safety guidelines and procedures is critical. Confusion can lead to mistakes and accidents, emphasizing the importance of reporting safety concerns.
➤ Training: Regular safety training is crucial. Employees must understand the risks associated with their roles and the ways to mitigate them.
➤ Workload and Staffing: Overworked employees or insufficient staffing can lead to fatigue, stress, and errors, which in turn increase the risk of accidents.
➤ Policies and Procedures: Well-defined and enforceable safety policies and procedures can significantly mitigate accident risk.
➤ Leadership: Leaders should exemplify safe behavior, show commitment to safety in their actions, and engage with employees about safety matters.
Addressing these organizational factors requires commitment from all levels of the organization, from the highest levels of management down to each individual worker. It involves fostering a strong safety culture, ensuring effective communication and training, managing workloads, establishing clear policies and procedures, and demonstrating strong safety leadership.
In conclusion, the Odisha train accident of June 2nd, 2023, underlines the importance of recognizing and mitigating human, environmental, and organizational factors in the workplace. Ensuring safety is a collective responsibility requiring everyone's vigilance, adequate resources, and a strong safety culture.
The lesson from this incident is clear: the price of neglecting these elements is simply too high.
Comments